We all have encountered situations where an unidentified problem halts a seamless process, and we try to analyze the reason for it by identifying its core or “root cause”.
A root cause is the core issue that puts the entire cause-and-effect reaction in motion, ultimately leading to the problem(s). The Root Cause Analysis (RCA) of an issue is an effective way of adequately treating a problem than merely treating its symptoms.
We are going to cover the following topics in this article:
- History of Root Cause Analysis
- Root Cause Analysis Explained
- Root Cause Analysis Tools and Techniques
- Root Cause Analysis Best Practices
So, let’s dive right into it.
History of Root Cause Analysis
Before becoming a widely accepted analysis tool, Root Cause Analysis first appeared in engineering. The evolution of this method is credited to the founder of Toyota Industries Co., Ltd., Sakichi Toyoda. Famously called the ‘King of Japanese Inventors’ and the ‘Japanese Thomas Edison’, he was a revolutionary personality, and his numerous inventions speak volumes about his contributions. Among his various contributions, identifying the root cause of the problems and preventing detrimental situations is the most widely accepted one.
From the work of Toyota, the Root Cause Analysis process became popular, and gradually other industries started adopting and evolving with this problem-solving method. RCA found its users irrespective of the nature of the sector. E.g., the occupational health and safety industry used this process to examine events involving accidents. Similarly, the manufacturing industry used RCA to detect production failures.
What is Root Cause Analysis?
Root Cause Analysis is not a clearly defined methodology but a problem-solving process for investigating an identified incident, problem, concern, or nonconformity.
Root Cause Analysis is a process of performing systematic analysis to uncover the fundamental or deep-seated causes of an incident, failure, or problem.
RCA facilitates continuous improvement (of processes and systems) and improves business by identifying ways to resolve problems that lead to process failures.
As the user evolves with the process of root cause analysis, its use changes from reactive (performing RCA once the incident has occurred) to proactive (performing RCA to avoid an incident) so that problems are forecasted ahead of time.
Based on the domain it’s being applied, root cause analysis can be broadly classified as:
- Safety-based root cause analysis: Mainly used for accident analyses, safety, and healthcare.
- Production-based root cause analysis: Primarily used in quality control and industrial manufacturing.
- Process-based root cause analysis: Used as a follow-up from production and business processes.
- Failure-based root cause analysis: Typically used in engineering and maintenance.
- Systems-based root cause analysis: Putting together the ideas from change management, risk management, and systems analysis, this process is the merger of the approaches mentioned above
How to Perform Root Cause Analysis
The primary goal of Root Cause Analysis is to identify the underlying cause of a problem, which, in turn, results in benefits such as improving the quality of the products and services. However, RCA must be performed systematically to ensure the intended benefits are achieved.
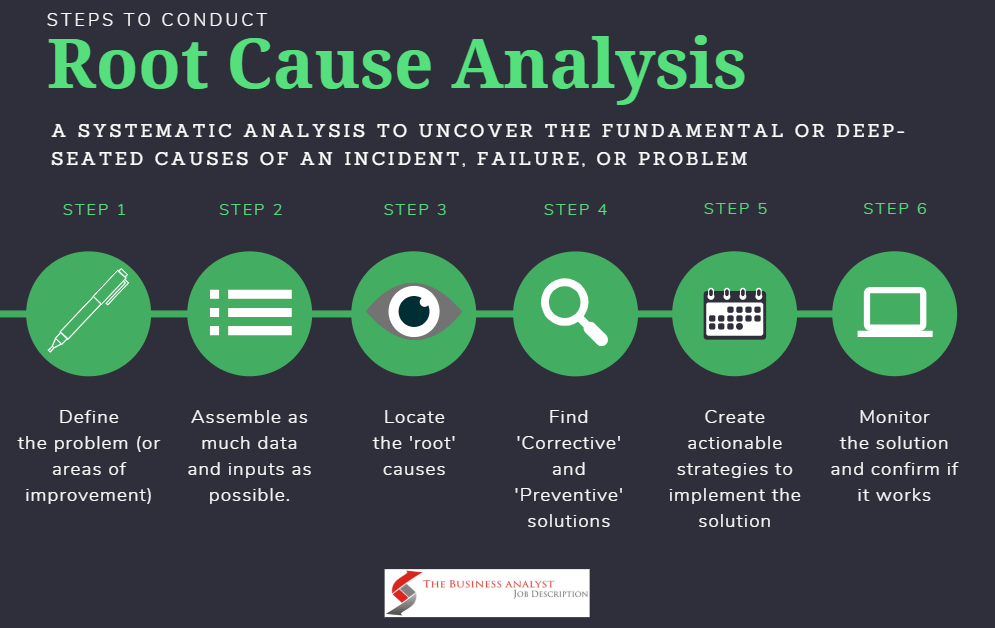
The individual/team conducting the RCA must stay on each step and exhaust all the possibilities before advancing to the next. So, while there are different techniques in establishing the primary problem, the underlying hierarchy to conduct the RCA remains the same, which is:
Step 1: Define the problem (or areas of improvement)
A problem well-defined is a problem half-solved!
The very first step is to ‘specifically’ and ‘clearly’ define the issue at hand in the form of the ‘problem definition’. Once outlined, stakeholders involved in the RCA process should review the problem definition for its accuracy and viability.
Step 2: Assemble as much data and inputs as possible.
You can’t find what you don’t know.
Next, one should gather enough information/evidence around the problem statement to understand the problem comprehensively. Try to seek as much qualitative and quantitative data about the problem statement as possible.
This step uses the Root Cause Analysis tools and techniques elaborated below.
Step 3: Locate the causes
With enough data available to you, now you should review each of the causes identified and try to pinpoint the underlined/root cause behind the issue. Again, the tools and techniques below will be of assistance.
Step 4: Find the solutions
This step is about coming up with a resolution for the root cause identified above. The solution could be:
- Corrective Solution: A short-term or stopgap measure to tackle the problem at hand. This solution addresses the ‘direct’ and ‘evident’ causes of the issue.
- Preventive Solution: A more thought-about and long-term resolution that targets the ‘root cause’ and prevents it from re-occurring.
Step 5: Create actionable strategies (or plans) to implement the solution
With the solution defined, it’s time to devise a plan to incorporate the solution methodically. This step will involve identifying and recording:
- activities required to implement the solution
- resources needed for the activities
- schedule of activities
- users responsible for the activities
- any additional aspects around the solution’s implementation
Step 6: Monitor the solution and confirm if it works
The last and quite essential step in the RCA process is to regularly monitor the solution post its implementation and ensure it stays viable and doesn’t let the root cause re-occur.
Root Cause Analysis Tools, Techniques & Methods
Once an organization identifies the root cause of a problem, the next step is to choose the correct RCA technique to get rid of it. To conduct Root Cause Analysis, there are a handful of established techniques and methods; however, it’s imperative to know how to use and correctly apply them.
Let’s take a deep dive into understanding each one of the Root Cause Analysis techniques in detail.
1. ‘5 Whys’ Analysis
5 Whys analysis is a popular root cause analysis technique that involves asking multiple follow-up questions regarding the problem. The number of “Why’s” can be five or more. By following this technique, one can delve deeper into the problem only to find that the answers to the questions are interrelated.
5 Whys Analysis, despite being a simple technique, helps clarify the ambiguity around the issue, creates a clearer picture, and strategically identifies the real cause of the problem.
<<< Featured Article: 5 Whys Technique: Basics, Examples, and Tips >>>
Example:
Implementation of the 5 Whys analysis technique is driven by a questioning outlook towards problems and not taking them at their face value. It is important to note that we are not asking just 5 random questions – the answer to each question should lead to the next question.
To understand the 5 Whys analysis, let’s take an example from the manufacturing domain.
Problem statement: The conveyor belt on the main production line has stopped.
1. Why has the conveyor belt stopped?
The main pulley responsible for rotating the belt is not functioning properly
2. Why is the main pulley not functioning correctly?
Because it’s not getting enough power from the motor
3. Why is it not getting enough power from the motor?
Because the motor has stopped working
4. Why has the motor stopped working?
Because the motor windings had burned out
5. Why have the windings burned out?
Because the motor was loaded beyond its power capacity
6. Why was the motor overloaded?
Although there were specifications about the permitted load frequency every hour, there were no instructions about the maximum load weight.
So you see, we needed 6 Whys to finally decipher that the weight of the load on the motor was more than its capacity, and now we either need to replace the motor with a more powerful one or restrict the maximum load weight permitted on the conveyor belt at a time.
The 5 Why technique is quite popular in its usage as its implementation does not require any specialized knowledge or resources. However, more sophisticated methods (discussed below) are needed while tackling complex RCAs.
2. Failure Mode and Effects Analysis (FMEA)
FMEA technique is used to determine the failures within a design or a process and can be applied at any level – planning, designing, implementation, or inspection.
Failure Mode and Effects Analysis (FMEA) helps prioritize the failure modes and recommends corrective measures to avoid catastrophic failures and improve quality. If you noticed, there are two specific aspects of FMEA, i.e.:
- Failure Mode: It involves identifying different ways, types (or modes) in which something can fail
- Effects Analysis: It consists in analyzing the effects and consequences of each of the failure modes
Example: In Acme’s aluminum coil manufacturing unit, there was a vibration problem inherent in one of the mixer units. Now FMEA analysis was conducted to identify the different failure modes, their effects, and possible causes. The investigation resulted in preventive and corrective action recommendations for the problem:
- Preventive action: Implementation of monthly maintenance to ensure proper functioning and reliability of the machines. Furthermore, responsible authorities were instructed to carefully follow the monthly maintenance guidelines for each machine and document the data in the monthly maintenance report.
- Corrective action: Balance the mixer blades and replace the bearings
Thus, as we just saw in the above example, the systematic implementation of the FMEA technique resulted in the improvement of the durability of the machine and also increased the overall productivity of the manufacturing unit.
Used by many companies, FMEA, as a root cause analysis tool, efficiently detects faulty parts of a process that require correction. FMEA can:
- Find the frequency of the failures occurring,
- Suggest remedial actions be implemented to prevent future occurrence of such failures, and
- Check the effectiveness of the measures taken
3. Fishbone Diagram / Cause-and-Effect Diagram (CED)
One of the most widely used tools to conduct complex root cause analysis is the Ishikawa diagram, Fishbone Diagram, or the Cause-and-Effect Diagram (CED). This tool is used in situations when the root cause is entirely unknown.
Cause-and-Effect Diagrams uncover ‘all’ the potential root causes associated with a specific issue from the outset of the analysis.
To conduct analysis using the fishbone diagram, a fish’s skeleton-shaped design is created with the problem at the head of the fish and significant causes of the problem as branches off its spine. Then, each of the ‘branches’ is taken one at a time, and its causes are identified through questioning and brainstorming. These causes form the sub-branches of the spine.
To facilitate the analysis, the following generic causes/categories may be used for a start:
- Machine/equipment/technology
- People/manpower
- Methods/process/systems
- Materials/consumables
- Environment/surroundings
Example: An excellent example of root cause analysis using the Fishbone technique is in the Information Technology (IT) industry.
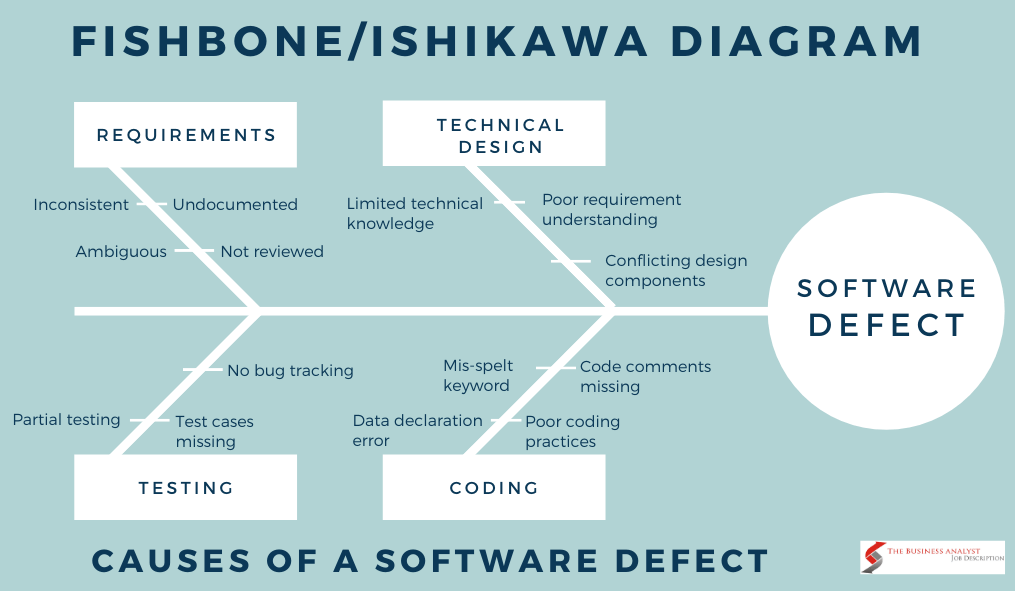
For instance, let’s consider a situation where a major bug is reported in software being built during its User Acceptance Testing (UAT) phase. To uncover the root cause of this incident and not just to rectify the issue on the surface, the Project Manager and/or the team would create the following primary ‘fishbone’ categories:
- Requirements
- Technical Design
- Coding
- Testing
Post the identification of the primary categories comes the brainstorming. Since there can be situations related to each of the above main categories that would have led to the incident, the PM should now scrutinize and find out as many possible causes that may be related to those categories.
Some questions that could be asked are:
- Were the requirements reviewed?
- Did the technical design team have a complete understanding of the software requirements?
- Were correct coding practices followed while developing the application?
- Were the test cases created for all the requirements?
- If it were confirmed that the Testing category is contributing to the problem, then the fishbone diagram would need to be expanded again with new branches formed to uncover which aspect of the ‘Testing’ category resulted in the root cause.
So, with the above example, it is seen that root cause analysis is more brainstorm-y in nature; however, it can help gather all the potential causes on the table.
4. Pareto Analysis
Pareto analysis is another helpful technique to conduct RCA when trying to identify the factors causing the most issues. Pareto analysis is also called the Pareto chart or Pareto diagram.
Pareto analysis is based on the Pareto Principle, which states, “For many events, roughly 80% of the effects come from 20% of the causes”.
While using the Pareto analysis for RCA, the intention is to identify the prominent cause(s) contributing the most to the problem at hand by studying and evaluating the quantitative data available for the causes.
Let’s take a quick look at how to perform Pareto analysis:
- Define the problem statement
- Identify the activities/causes that are contributing to the problem and need assessment
- Plot each cause on a bar graph and on the X-axis
- Take one cause at a time and assess its impact towards ‘causing’ the problem. Quantify this impact as a ‘score’ and plot the same on Y-axis.
- Carry out the same activity (in step 4) for all the causes identified in step 2.
- Rearrange the causes in descending order of their scores
Note – When dealing with many causes, it’s a good idea to group similar causes in categories and then carry out the Pareto analysis for each of those categories.
Now, with the Pareto chart you just created, you can immediately identify the activities/causes that need to be tackled to resolve the root cause.
Root Cause Analysis Best practices
Re-occurring failure of events in a process negatively affects the safety, production, or maintenance of the connected resources, which in turn, affects the overall profitability.
Specific best practices should be considered while performing a thorough root cause analysis. Adopting these best practices ensures the identification of the root cause of the problem and helps define specific and sustaining corrective actions.
- Focus on rectifying the actual cause of the problem rather than its symptoms
- There could be multiple root causes that might be interrelated
- Questions ‘how’ and ‘why’ some unwanted events have taken place rather than ‘who’ was responsible for the undesirable activity i.e. question ‘processes’ and not people
- Tackle the problem methodically to find concrete cause-effect evidence to back up the root cause claims
- The people participating in the analysis should have a sound knowledge of the different RCA methods and their application
- The identified root cause should have the consensus of the team participating in the analysis activity
- The implementation cost should be kept in mind while determining a solution to a problem
- Acknowledge the fact that the solution to a root cause could have cultural implications and its implementation might face resistance from the people affected
- Visualize your data – Visualization helps with quick analysis and investigation
- The complete process should be moderated by a facilitator having considerable experience conducting and guiding RCAs
Summary
Root cause analysis is undoubtedly a highly recommended practice for conducting multidimensional analysis when something goes wrong within a defined process. The success of RCA depends on how effectively the root cause of a problem is detected.
Since exploring the problem from every dimension can help identify the root cause, RCA always encourages its users to ask ample questions and gather as many points of view as possible. Each of these viewpoints is then investigated and reviewed to identify all the probable causes of the problem.
There are different types of tools and methods used for Root Cause Analysis. These techniques help businesses resolve complex and intricate situations by finding the best possible solutions. Though a single individual can carry out root cause analysis by themselves, in most cases, a team approach is the right one. Irrespective of the industry, applications of Root Cause Analysis are endless as they can help enterprises effectively prevent the recurrence of failures and anomalies along with significantly improving the efficiency of business processes.
FREE KIT DOWNLOAD: Get BA Documents Template Toolkit!!
Our free Template Toolkit contains the following professional, pre-formatted, and ready-to-use Business Analyst Document templates:
- Use Case Document Template
- Requirement Traceability Matrix (RTM) Template
- Requirement Management Plan Template
- Project Vision Document Template
- Test Case Template